The tractor of the future: connectivity and electrification
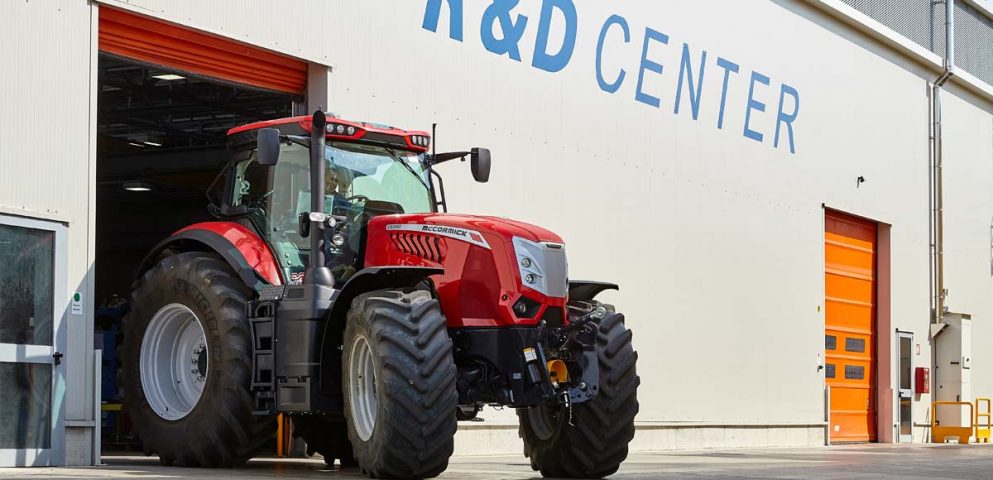
Designing the future by building on the work done over the past 20 years.
With this vision, we continue on our constant path of developing ever more advanced tractors. In this article, let’s see together what we should expect in the near future and what are the most important developments that will affect the construction of the new generation of tractors.
Table of contents
Reducing emissions: a new and exciting challenge
Improving productivity and operator comfort
Electronics: contributing to a simplified driving system
Agriculture 4.0: new solutions for new needs
ISObus: between present and future
Electric power: an ever closer goa
Reducing emissions: a new and exciting challenge
Without doubt, among the most significant developments are those related to engines, which go hand in hand with the need for a gradual but necessary reduction in environmental emissions.
In the words of Giovanni Esposito, Innovation Director at Argo Tractors, the adaptation of engines to national and European regulations is what has marked the development process in recent years.
This was a considerable challenge for the manufacturers, who had to carry out a complete revision of their vehicles with every adjustment. This meant and still means a new and complete design of the distribution of the volumes of the tractors in order to add the new exhaust gas treatment systems, while maintaining the characteristics of the machine intact.
We talked about sustainable agriculture in this article:
Improving productivity and operator comfort
Today, medium-high power tractors have undergone an important transformation in their use: in addition to the more classic open field operations, the hours of work used for transport are up to more than 50% of the total working time
This makes it essential to make improvements in relation to
- productivity and speed of the vehicles
- operator comfort.
In the face of this change, tractors are already being equipped with increasingly sophisticated suspension systems and speeds, where permitted, may reach up to 60 km per hour.
Electronics: contributing to a simplified driving system
The electronic and control systems have made driving the tractor easier and more comfortable, partly due to the elimination of the various mechanical levers in the cab that meant the tractor had to be packed with equipment.
Almost all modern tractors today are equipped with joysticks and buttons placed on a comfortable and functional armrest.
“The presence of Drive by wire electric controls – explains Giovanni Esposito – increasingly represents the state of the art of tractors intended for professional users, such as contractors and large companies that use the vehicles for many hours and need high performance”.
An enormous benefit to this category of users also comes from the continuously variable transmission. This innovation has made it possible, through the electronic management of the systems, to obtain the very best interaction between transmission and engine, optimising the availability of power and fuel consumption in every work situation
Agriculture 4.0: new solutions for new needs
Agriculture 4.0, the natural evolution of precision farming is now a reality:
- possibility to manage almost all tractor parts electronically
- possibility to control the tractor implements via ISObus
- make vehicle data available with connectivity on the cloud
The possibilities offered by connectivity are countless, from the control of working parameters, to fuel consumption, to geolocation, and even the “driving style”, with the possibility of evaluating the ability of each specific user of the vehicle.
Connectivity and the availability of data make diagnosis systems and the training of specialised personnel even more efficient, so that they can handle any eventuality.
Early servicing, even remotely, and sometimes in a predictive manner, is no longer a future hypothesis, but something that is already happening.
ISObus: between present and future
Today we are increasingly moving in the direction of interconnected machines to optimise work.
This is helped by the ISObus, a proven system that makes it possible to digitally control the implement and apply the concepts of Precision Farming,
and which is evolving towards the TIM (Tractor Implement Management) system, an advanced ISObus where, unlike the traditional ISObus, it is the implement that influences specific tractor parameters with the aim of specifically optimising the tractor/implement combination.
Electric power: an ever closer goal
Finally, the electrification process is on the agenda.
“Argo Tractors,” says Esposito, “recently presented the Electra – Evolving Hybrid – tractor, a hybrid system that combines an i.c. engine (on the rear wheels) with electric drive (on the tractor’s front wheels). The system allows the speed of the front and rear wheels to be managed separately, giving the vehicle greater stability while ensuring optimum manoeuvrability”.
While a full-electric range of tractors is still unthinkable, especially in the high-power range where battery volumes would need to be much larger than those of the tractor itself and charging times would be long, the situation could be different for low-power vehicles and specialised tractors, where the use of power is still crucial but expended differently.
In the near future, everything will depend on developments that will have to deal with reducing the costs and volumes of batteries currently on the market.